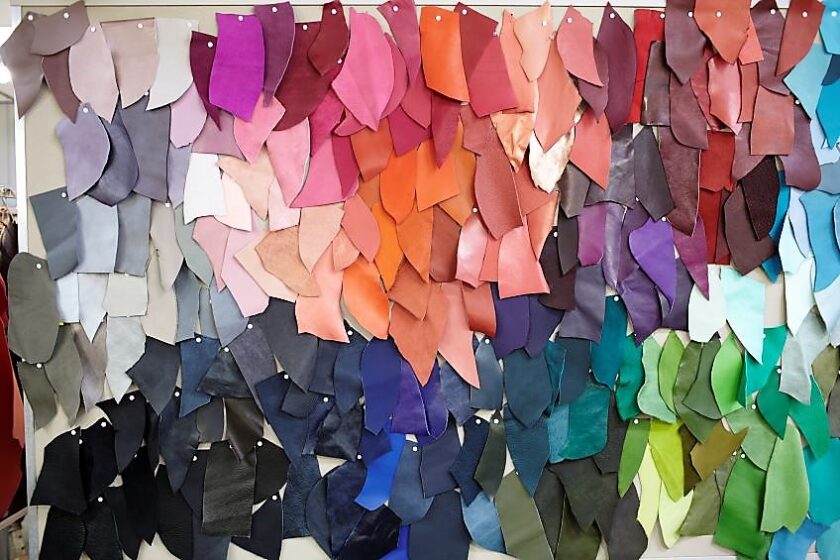
Thanks to new processes and technologies, the leather production industry has cut its water footprint by 37% in the past 25 years and it’s improving all the time.
Read on to discover more about the innovation that is reducing tanneries’ water usage by up to 40% whilst lowering their chemical use. And trace the industry’s first steps towards water-free tanning as it makes good on its commitment to provide a slow style alternative to the wastefulness of fast fashion.
By Stephen Sothmann, President of the Leather and Hide Council of America (LHCA)
Water is a vital resource – crucial for the survival of every living thing, intrinsic to agriculture and industry and a critical component in leather production. But there is only so much of it to go around, with evidence suggesting that two-thirds of the world population could be living in water-stressed countries by 2025 if current consumption patterns continue.
The leather industry is keenly aware of the need to use this precious resource more efficiently to meet legal requirements or guidelines as well as its own quest for sustainability. Its efforts have paid off and, thanks to new processes and technology innovations, it has reduced its water footprint by more than 35% in the past 25 years.
As important as water is, or has traditionally been, in the leather making process, some tanners and leather manufacturers have proved that it’s possible to achieve the same leather look and feel using far less water than before. And they’ve shown that doing so leads to additional benefits, further improving leather’s environmental credentials.
Soaking without soaking
One way to reduce water use in leather is to tan the hide immediately after slaughter. Traditionally, hides are salted or brined to preserve them until they can be further processed into leather. The initial beamhouse operations includes liming and washing the hide to remove the salt before tanning.
Today, a growing number of tanners are processing the fresh hides immediately, eliminating the need to use salt as a preservative and to remove the salt through a freshwater wash. This initial tanning realigns the cellular structure of the hide to create the first stage of a leather product, often called wet blue because of its color. The United States, a major hide supplier, has increased exports of wet blue from about 10-15% of production in the early 1990s to more than 30% in 2020. Most of this wet blue is created from raw hides.
Using fresh hides also reduces salt in the wastewater. “Salt in the effluent is more and more of a problem because it can’t be cleaned easily,” says Thomas Heinen, CEO of German tanner and outdoor footwear specialist Heinen Leather, whose clients include Lowa, Meindl, and Clarks.
Reducing wastewater pollution is a moral imperative and legal requirement for the global leather industry. Using less salt in the process is one way the industry is meeting this challenge directly.
The small spheres making a big difference
Another innovation helping tanners do things differently and more water-efficiently is Sferes. Developed by Qualus, these polymer balls about the size of jelly beans replace over 30% of the water needed for the tanning and retanning (secondary tanning) process.
Sferes work by driving chemicals deep into the fiber structure of the hides. This means that not only less water but also less chemicals are needed, leading to a reduction in effluent and wastewater processing. Also, Qualus has developed a proprietary cleaning system that removes the residual leather fibers and dyes from the surface of the Sferes so that they can be used all over again – continuing the cycle of benefits.
Lefarc, one of the most sustainable tanneries in Mexico, has been taking advantage of these sphere-shaped innovations for the past year to produce leather for brands including Timberland and Wolverine.
“By employing this technology, we can produce leather more sustainably, delivering better aesthetics and improving its physical properties,” says Francisco Rios Warren, Lefarc’s head of commercial.
“Additionally, we have reduced our water use by between 30 and 40% while maintaining our quality standards and improving the condition of our wastewater.”
Towards water-free tanning
ECCO Leather (ECCO), the global footwear brand, is going even further with what it describes as “the first solid step towards water-free leather manufacturing” with its DriTan Technology.
The breakthrough process uses the moisture already present in hides in the tanning process. According to the company, implementing the technology in its tannery in The Netherlands saves 20 liters of water per hide, or 25 million liters annually. It also minimizes the use of chemicals and reduces effluent; the company reports eliminating 600 tons of sludge, roughly 40 truckloads, from landfill per year, without any drop-off in the quality of the leather produced.
Thomas Gøgsig, Head of Applied Research at ECCO, notes:
“It took a lot of research, investment and manpower – a strong cocktail of science, know-how and traditional craft.”
“But the biggest challenge was in opening our eyes. Tanning is a very old and traditional industry, so people tend to forget to ask: Can it be done differently?”
ECCO is actively working to spread the benefits of this water-saving innovation. The latest iteration, DriTan 2.0, has now been fully implemented at the company’s tannery in Indonesia and is in the process of being implemented in other facilities.
Reduce, reuse, recycle
The leather industry doesn’t only consider the amount of water it uses, but also the quality of water it discharges into the environment. In many countries, tanning and finishing are strictly regulated and companies are required to comply with stringent wastewater requirements. In Europe, where EU regulations eliminate solid waste disposal, tanning facilities are experimenting by reclaiming their water and reusing it in the tanning process. In addition, they are further processing the sludge for use as a fertilizer, a mixer for cement or an alternative energy source.
The Scottish Leather Group (SLG), for instance, a leading supplier to the European aviation industry, treats and then recycles 40% of its wastewater back into the production process.
The net result of the industry’s smarter processes and use of technology innovations is less water, cleaner water and a much more sustainable manufacturing process.
Leather may be one of the oldest industries in the world but if it keeps on innovating and adapting the way it has done in the past 25 years, there’s no knowing what it might achieve in the future. ECCO’s vision of water-free leather manufacturing might not be too far-fetched after all.
This is article was developed in support of Real Leather. Stay Different. – a campaign to promote the sustainable qualities of leather and champion slow style. It first appeared on sustainfashion.info.
Main photo courtesy of ECCO Leather.